Technique : Le freinage
le 12/02/2009
LES FREINS A TAMBOUR
En examinant les forces qui s'exercent sur les mâchoires on remarque que sur le segment de gauche, la force tangentielle Tg donne naissance à un moment par rapport à l'axe de pivotement du segment qui est de même sens que le moment de la force de serrage Sg tandis que sur le segment de droite la force Td, s'oppose à l'action de la force Sg.
Pour des efforts de serrage identiques (Sg, = Sd ). la force exercée à gauche sera plus élevée que celle de droite : on dit qu'il s'exerce un effet d'auto-serrage . Pour utiliser celui-ci sur les deux mâchoires, on déplace le point fixe et le piston de commande du segment de droite .
Le raisonnement est valable pour un certain sens de rotation du tambour, mais lorsque la rotation se produit en sens contraire (marche arrière), les segments provoquent tous un effet d'autodesserrage. L'extrémité du segment non soumise à l'effort de serrage peut être articulée de diverses manières sur le flasque :
- avec un axe d'articulation,
- une biellette,
- ou encore un simple plan incliné sur lequel l'extrémité du segment prend appui librement.
Cette dernière solution est appelée segments flottafis ou autocentreurs. Elle permet le centrage du segment dans le tambour. donc une distribution plus uniforme du freinage. Il existe également des segments à double expansion (cylindres de commande aux deux extrémités)
Les pivots des freins à tambour simples ont une forme excentrique, ce qui permet le centrage facile des segments par rapport au tambour et le rattrapage du jeu. Les principaux problèmes posés par les freins à tambour sont identiques à ceux des freins à disque.
Il faut tout d'abord considérer le refroidissement. étant donné l'influence de la température sur le coefficient de frottement et la qualité des garnitures. La pression doit être limitée pour ne pas user trop vite les surfaces de contact. On exige en principe des tambours les caractéristiques suivantes :
- La légèreté, afin de réduire les masses non suspendues là cet effet, on monte parfois les tambours en sortie de différentiel ;
- La résistance à l'abrasion ;
- Une bonne conductibilité thermique, afin d'évacuer rapidement la chaleur produite pendant le freinage et de réduire la température des garnitures.
Les tambours sont construits en alliage d'aluminium (légèreté et bonne conductibilité thermique) ou en fonte (grande résistance à l'abrasion). La résistance à l'abrasion de l'alliage léger étant faible, on prévoit généralement, dans le premier cas, une couronne intérieure rapportée en fonte.
Pour dissiper plus rapidement la chaleur, on augmente souvent la surface de déperdition en munissant le tambour d'une série d'ailettes extérieures, accroissant en même temps sa rigidité.
Ces ailettes seront quelquefois disposées en hélice pour créer un effet de ventilation (Alfa Roméo 1900 Spider de 1954).
Les segments devant être légers (afin de réduire les masses non suspendues) tout en étant rigides (pour éviter les déformations élastiques au freinage) sont généralement réalisés en alliage d'aluminium ou en tôle d'acier soudée. Ils sont revêtus d'une garniture de frottement à base d'amiante dans laquelle sont noyés des éléments métalliques (fils ou copeaux d'alliage de cuivre ou d'aluminium) qui lui confèrent une résistance mécanique élevée (charge de rupture à la compression 560 kgp/cm2) et une bonne conductibilité thermique.
Les garnitures de freinage doivent présenter les caractéristiques suivantes :
- Un coefficient de frottement élevé (0,3 à 0,4) peu sensible à la température ;
- Une bonne résistance à l'abrasion et au cisaillement.
La fixation au segment est réalisée au moyen de rivets en alliage de cuivre ou d'aluminium, dont la tête doit être en retrait par rapport à la surface extérieure de la garniture pour assurer une certaine marge d'usure.
Très souvent, surtout dans les applications les plus modernes, les garnitures sont collées : la fixation est ainsi supérieure ; l'évacuation de la chaleur plus efficace ; enfin, toute l'épaisseur de la garniture peut être utilisée puisque le problème de l'encombrement des têtes de rivets n'existe plus.
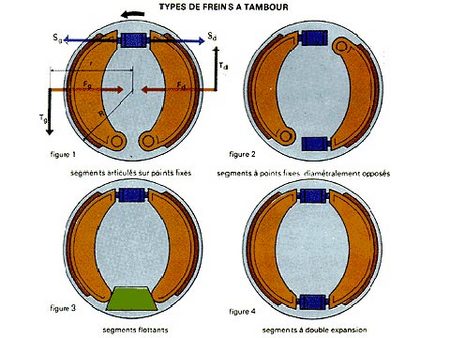
D.R.
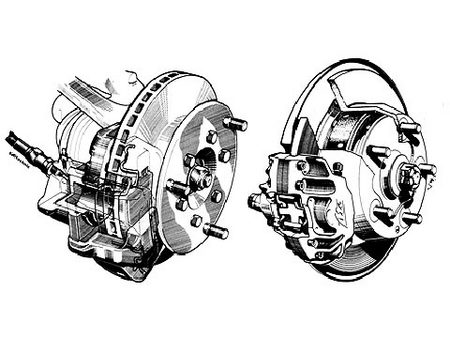
D.R.
LES FREINS A DISQUE
Ils apparurent pour la première fois en 1902 sur une Lanchester 18 HP, mais avec des résultats peu satisfaisants faute de matériaux adéquats.
Au début des années vingt, les freins à disques trouvèrent quelques applications sur les tramways de quelques villes européennes, entre autres Paris, Rome et Berlin. Ils étaient constitués par deux disques opposés sur les faces internes desquels agissaient des plaquettes de frottement.
Pendant la Seconde Guerre mondiale, quelques projets furent conçus pour des véhicules blindés ou des avions. Ces derniers devaient être capables de dissiper, après l'atterrissage, d'énormes quantités d'énergie cinétique.
En 1953, après des années de recherches et d'essais, les techniciens de Dunlop réussirent à mettre au point des freins à disque. Utilisés pour la première fois aux Vingt-Quatre Heures du Mans, ils connurent la victoire avec la Jaguar XK 120 de Rolt et Hamilton, qui s'adjugea en outre le record de la distance (4088,600 km contre 3 733,800 km parcourus l'année précédente par Mercedes).
Les avantages présentés par ces nouveaux freins étaient de nature à les faire rapidement imposer malgré des tentatives d'amélioration des freins à tambour.
Dés la fin des années cinquante, les freins à disque équipèrent un nombre toujours croissant de voitures pour être finalement universellement utilisés.
Un frein à disque se compose d'une partie fixe : l'étrier, solidaire des structures du véhicule, et d'une partie mobile : le disque, entraîné par la roue. L'étrier supporte les deux plaquettes qui, sous l'action d'une commande généralement hydraulique, pressent le disque, empêchant ainsi sa rotation. Les plaquettes sont toujours maintenues en léger contact ou à très courte distance (0,20 à 0,25 mm) du disque.
A la fin du freinage, le rappel est assuré par des ressorts à réglage automatique, ou encore, plus simplement, par l'élasticité de la bague d'étanchéité en caoutchouc du cylindre de commande.
Dans ce dernier cas, au fur et à mesure que la garniture de frottement s'use, le piston de poussée effectue des courses toujours plus grandes jusqu'au moment où, ayant dépassé la course permise par la déformabilité de la bague d'étanchéité, il glisse sur celle-ci et trouve automatiquement sa nouvelle position : on obtient ainsi un réglage automatique.
Le fait que les plaquettes soient en léger contact avec le disque n'entraîne aucun inconvénient puisqu'elles sont parallèles à sa surface et qu'une faible pression est suffisante pour exercer l'action de freinage.
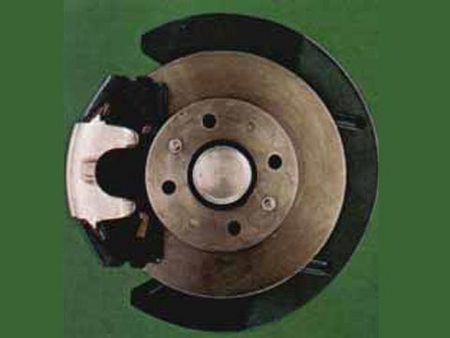
D.R.
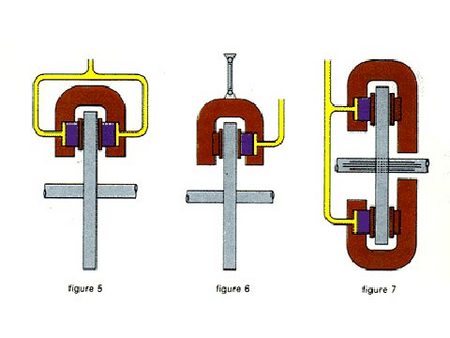
D.R.
Dans les tambours, au contraire, la mise en contact entre les segments et le tambour se produit avec seulement une légère rotation et le contact s'accentue instantanément avec des segments autoserrants.
Les garnitures ne doivent donc pas lécher le tambour à l'arrêt.
En ce qui concerne le système de fixation du disque et de l'étrier, on peut rencontrer les cas suivants :
- Montage axial. La pression du circuit hydraulique de commande pousse les deux plaquettes contre le disque (fig 5) ;
- Une des deux plaquettes est fixée rigidement sur l'étrier, tandis que l'autre est commandée par un piston hydraulique. Lorsque la poussée s'exerce sur la plaquette mobile, la réaction fait déplacer axialement l'étrier du côté opposé, conduisant l'autre plaquette au contact du disque. Un tel étrier est dit flottant (fig. 6) ;
- Le disque est mobile axialement avec un étrier fixe. (fig 7) Une plaquette est solidaire de l'étrier ; l'autre, commandée par le piston, vient en contact avec le disque et le pousse 'contre la première . La position des étriers peut être soit en avant, soit en arrière de l'axe de rotation de la roue.
Chaque solution correspond à des conditions de charge précises pour les roulements des roues.
Dans le cas d'un étrier disposé en avant, la réaction due au frottement étrier-disque est dirigée vers le haut et s'ajoute par conséquent à la réaction verticale due au poids, ce qui surcharge les roulements.
Si, au contraire, l'étrier est disposé en arrière, la réaction est dirigée vers le bas et se soustrait de la réaction verticale due au poids, ce qui soulage les roulements.
Les disques de freins doivent présenter, en règle générale, des caractéristiques analogues à celles des tambours :
- légèreté,
- résistance à l'usure
- et bonne conductibilité thermique.
Ils sont normalement réalisés en fonte spéciale au chrome/ molybdéne, très résistante à l'usure. A chaud, en présence de projection d'eau, les disques en fonte ne présentent pas d'inconvénients, tandis que ceux en acier sont sujets à des phénomènes de trempe qui ont pour conséquence leur fragilisation.
Les étriers doivent être être légers et rigides ; ils sont habituellement construits en alliage d'aluminium, quelquefois en alliage de magnésium ou encore en fonte. Les matériaux de frottement des freins à disque ont des caractéristiques analogues à celles des matériaux de frottement retenus pour les freins à tambour.
Il ne faut cependant pas oublier qu'ils sont soumis à des pressions plus élevées, la surface de contact étant plus petite (une garniture a, en moyenne, une surface de 30 à 35 cm2 contre les 55 à 60 cm2 des freins à tambour) et que le rayon de frottement est plus faible. Sur les modèles à hautes performances, on monte souvent des disques perforés qui aspirent l'air par le centre et le refoulent par la périphérie. Ces types de disques (communément appelés auto- ventilés) sont apparus vers la fin des années cinquante sur les voitures de compétition, puis en 1965 sur les voitures de série, plus précisément sur la Chevrolet Corvette.
Afin de réduire l'importance des masses non suspendues, on monte quelquefois les disques à la sortie du différentiel.
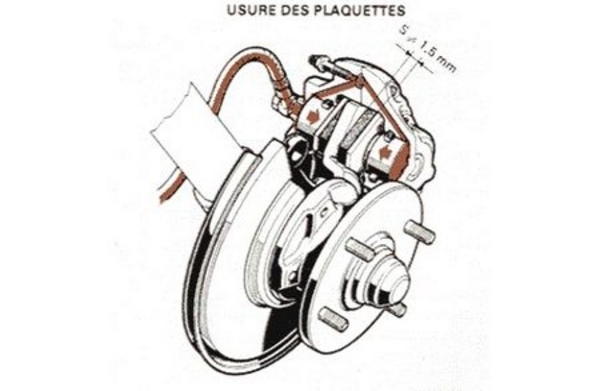
Usure des plaquettes D.R.
COMPARAISON ENTRE LES FREINS A TAMBOUR ET A DISQUE
Pour donner une idée des énormes progrès réalisés dans le freinage, on peut comparer les distances de freinage d'une Rolls Royce Phantom 1 de 1926 (voiture équipée de freins mécaniques à tambour sur les quatre roues avec servofrein mécanique) à celles des voitures modernes (freins à disque avec servofrein mécanique).
La première stoppait sur 32,40 m à 60 km/h et sur 49,40 m à 80 km/h, alors que les automobiles modernes freinent respectivement sur 8,20 et 35 m.
Malgré la supériorité des freins à disque, les freins à tambour présentent certains avantages :
- Leur rayon de frottement est généralement supérieur au rayon géométrique du tambour, tandis que dans les freins à disque il est inférieur au rayon du disque : par conséquent, pour une même force de frottement, le couple de freinage sera plus grand dans les freins à tambour ;
- Pour une même force de serrage, il est possible d'augmenter le couple de freinage en montant, par exemple, deux segments à enroulement, alors que, pour compenser l'infériorité mécanique des freins à disque, la pression de freinage doit être plus forte, ce qui oblige au montage d'un servo-frein même sur des véhicules de poids relativement modeste (les pressions dans le circuit hydraulique sont de 80 à 100 kgp/cm2 dans le cas des freins à disque, tandis qu'elles ne sont que 12 à 15 kgp/cm2 pour les freins à tambour). L'effort musculaire reste, par contre, limité pour les deux types à des valeurs de 25 à 35 kgp.
Par contre, la surface de contact des plaquettes sur le disque étant exposée à l'air, il est toujours possible de prévoir une canalisation.
Pour les freins à tambour, le refroidissement est beaucoup plus difficile, du fait que la partie extérieure seule est exposée à l'air, tandis que la chaleur est produite à l'intérieur.
Pour cette raison, les freins à disque étant plus facilement débarrassés de l'eau, de la poussière et de la boue seront beaucoup moins sensibles au fading (la poussière des garnitures déséquilibre les freins à tambour).
Avec un disque, l'usure des garnitures de freinage est régulière ; toute la surface des plaquettes frottant sur le disque, la distribution des pressions sera uniforme.
Dans les freins à tambour, l'usure est irrégulière, atteignant sa valeur maximale vers l'extrémité libre du segment. Ceci s'explique par la rotation qui caractérise le mouvement d'approche du segment pour venir en contact avec le tambour.
On pourra obtenir une distribution plus uniforme de l'usure avec des freins à segments flottants ou à double détente.
Les pressions spécifiques et les forces de frottement plus élevées dans les freins à disque ont pour conséquence une plus grande production de chaleur.
Pour éviter la formation de bulles de vapeur dans le cylindre, il faut utiliser un liquide de frein au point d'ébullition élevé (200 à 220 °C contre 150 à 160 °C pour l'huile des freins à tambour). La production de chaleur entraîne également des dilatations qui, bien que n'ayant aucune conséquence dans les freins à disque (le disque se dilate radialement), sont une source d'inconvénients dans les freins à tambour (la dilatation radiale du tambour est plus grande que celle des segments, ce qui, en augmentant le jeu tambour- segment, réduit l'effet de freinage).
Autre point positif pour les disques : les opérations de contrôle, d'entretien et le remplacement des plaquettes sont faciles. Les freins à disque se prêtent peu à l'utilisation comme freins de stationnement, la difficulté concerne particulièrement la réalisation d'une double commande : hydraulique pour le frein principal et mécanique pour le frein de stationnement. On prévoit parfois un frein à tambour placé à côté du frein principal à disque, ou encore un second étrier qui agira sur le même disque.
Il peut être intéressant d'établir une comparaison entre domaines d'utilisation en fonction de l'énergie cinétique absorbée par divers types de freins :
- Les freins à tambour sur les quatre roues sont utilisés dans les cas où les énergies cinétiques en jeu sont de l'ordre de 70 000 kgm (ce qui correspond, à titre indicatif, à des voitures de 900 kg circulant à 140 km/h) ;
- Les freins à disque sur les quatre roues sont utilisés pour l'intervalle approximatif des énergies cinétiques allant de 80 000 kgm (voitures de 900 kg à environ 150 km/h) jusqu'à 490 000 kgm (voitures de 1 600 kg à 280 km/h).
Pour une gamme de valeurs intermédiaire de l'énergie cinétique, le système mixte (freins à disque à l'avant et freins à tambour à l'arrière) est très répandu.
UTILISATION, ENTRETIEN ET PANNES
Il faut avant tout éviter le blocage ; donc adapter la pression sur la pédale aux conditions d'adhérence de la chaussée.
En virage, on doit prévoir une diminution de l'adhérence (une partie de celle-ci est utilisée pour la tenue de route longitudinale et l'autre pour la tenue transversale qui compte ici).
Dans ce cas, au freinage, la limite de blocage est atteinte beaucoup plus vite. Les équipements de freinage modernes comportent des dispositifs antiblocage sur l'essieu arrière par suite du transfert de charge qui se produit au freinage.
On monte généralement sur cet essieu des freins plus petits avec un limiteur de freinage qui réglera leur action en fonction de la charge.
Le lavage de la voiture et la traversée d'une grande flaque d'eau peuvent mouiller les surfaces de frottement, ce qui entraîne une perte d'efficacité.
Pour nettoyer les surfaces, il suffit alors de freiner doucement plusieurs fois.
Les freins d'un véhicule automobile doivent être régulièrement surveillés. Tous les 5000 km, l'épaisseur des garnitures de freinage doit être contrôlée en vérifiant en même temps l'étanchéité de la commande hydraulique.
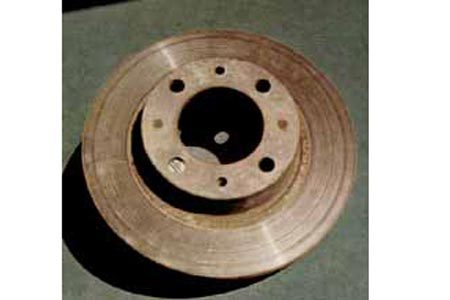
D.R.
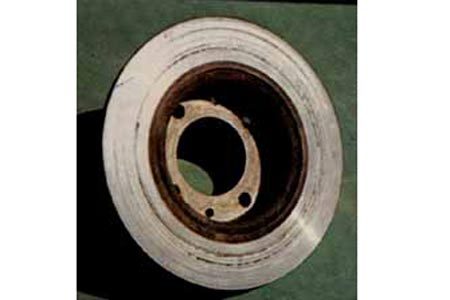
D.R.
Si l'épaisseur des garnitures est inférieure à 1,5 ou 2 mm, leur remplacement est nécessaire.
Signalons que les notices d'utilisation et d'entretien de beaucoup de constructeurs d'automobiles indiquent des limites d'usure de 7 à 8 mm pour les plaquettes de freins à disque, mais si l'on tient compte du fait que ces valeurs comprennent également l'épaisseur du support métallique de la garniture d'usure, après soustraction de cette épaisseur elles concordent avec celles indiquées ci-dessus.
Certaines installations possèdent un indicateur d'usure. Il s'agit d'un contact noyé dans le matériau de frottement qui, à un certain degré d'usure, ferme un circuit électrique, avec, pour conséquence, l'allumage d'un témoin sur le tableau de bord.
Avec une conduite correcte, les garnitures de freinage peuvent durer 80 000 km pour les freins à tambour et 40 000 km pour les freins à disque. A l'occasion de la vérification des garnitures, il convient également de contrôler l'état d'usure de la surface de frottement du tambour (une rectification permettra d'éliminer les ovalisations; il faut éviter d'augmenter le diamètre intérieur d'une quantité supérieure à 1 mm) et du disque, en vérifiant la perpendicularité de ses faces par rapport à l'axe de rotation.
Au freinage, la force d'inertie F appliquée au centre de gravité G provoque, sous l'effet du couple Fh, un transfert de charge de l'essieu AR sur l'essieu AV. Ce phénomène est indépendant de la rigidité des suspensions.
Pour les freins à tambour sans dispositifs de réglage automatique, il faudra rattraper périodiquement le jeu entre le tambour et les segments. Un jeu excessif se manifeste par une augmentation de la course de la pédale.
Le réglage se fait de la manière suivante : on fait tourner les excentriques prévus à cet effet jusqu'à amener les segments en contact avec le tambour ; on tourne ensuite lentement les excentriques dans le sens opposé, jusqu'à ce que la roue puisse tourner librement, sans aucun frottement ; enfin, on vérifie si le freinage est équilibré sur toutes les roues.
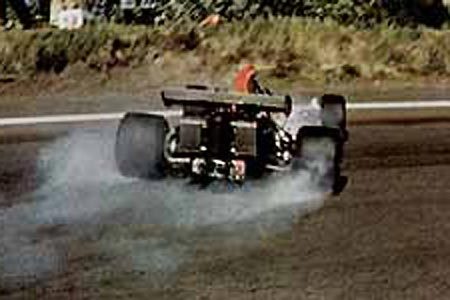
D.R.
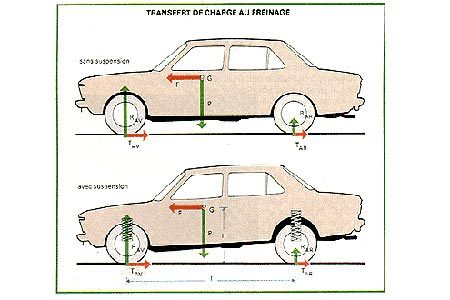
D.R.
La distance est mesurée à partir du moment où les freins entrent en action jusqu'à l'arrêt complet. Pour obtenir la distance de freinage, il faut additionner à cet espace la distance parcourue pendant le temps où se met en action le freinage (0,1 seconde environ).
Le coefficient d'adhérence est égal à 1 quand la force de frottement est égale au poids du véhicule. Ce coefficient peut atteindre 2,5 (force de frottement 2,5 fois supérieure au poids du véhicule) sur les autos de compétition équipés de pneus spéciaux sans sculptures.
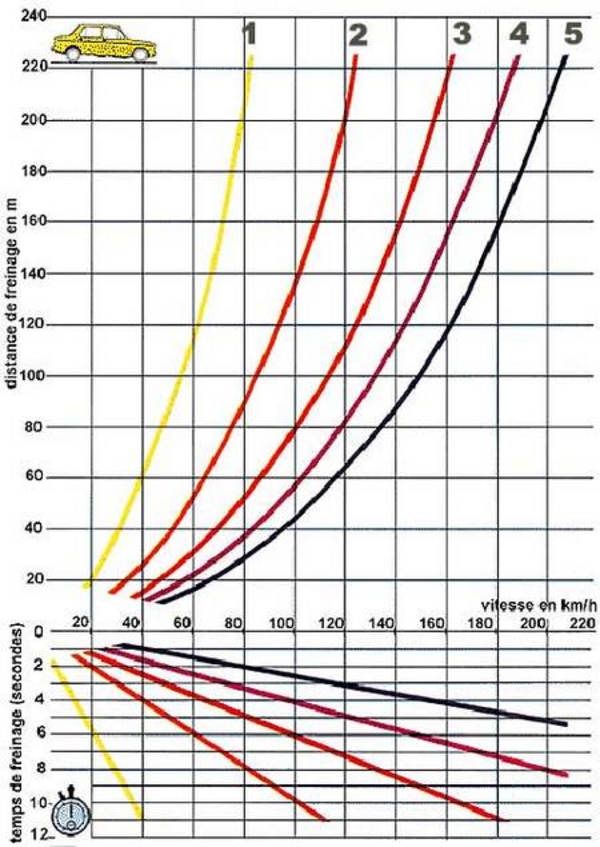
D.R.
1 : surface très glissante, boue, verglas, pneus lisses, aquaplaning. Coeff. : 0,1
2 : chaussée mouillée, pneus usés, gravillons, sable, roues bloquées. Coeff. : 0,3
3 : chaussée sèche, usure des pneus normale, chaussée humide mais granuleuse. Coeff. : 0,5
4 : chaussée sèche, bon gonflage, revêtement granuleux, pas de bloquage des roues. Coeff. : 0,7
5 : surface très rugueuse, pneus larges, bien gonflés, freinage contrôlé à la limite de l'adhérence. Coeff. : 0,9